In the previous episode (Issue 147) we dived into my past encounter with the name of Günter Pauler, and we now come back to the present event. Which is a shiny new DMM (direct metal mastering) dubplate disk from Stockfisch Records right here in my hands, my name on its label!
The fact that Günter Pauler is involved in this project (cutting a record directly to a metal disk) would have been enough on its own to get my attention. But in fact, there was something else about the idea of a DMM dubplate that had me drooling from excitement and I couldn’t wait to listen to it, my expectations already sky high.This is where my previous technical discussion of disk mastering technology becomes relevant. As a mastering engineer, I have always cut lacquer disks up to now. I never got into DMM. Regardless of the technology used, one of the challenges of the profession of a mastering engineer is to take test cuts to be played back on a regular turntable, to determine if the sound is as it should be. I have spent countless hours listening to my own test cuts on lacquer, which I then compare to test pressings, and the final pressings that come back from the pressing plant.
There is always a difference, but on a properly calibrated system, it can be kept small. I have documented differences as low as 0.1 dB in spectral content over a bandwidth of 20 Hz to 20 kHz between a test cut on a lacquer and the final pressing. So, if the plating and pressing are done with due care at a reputable facility, the differences between the master and the final product will be very small. However, the real shock came when I first got to listen to a metal mother made from my lacquer master, comparing this to both the test cut on lacquer and the final product. The metal mother simply sounds unbelievably better! Not only better than the final product, which is a few generation losses down the line, but also better than the lacquer test cut, which is upstream!
How is this even possible?
Well, this is not about the information that is actually recorded onto the medium, but about the information that can be extracted out of it again upon playback. Lacquer disks are extremely soft and fragile. Even after a single playback, the quality has already degraded. Ten playbacks are about as much as can be expected where sound quality matters.
But even more interestingly, apart from the permanent plastic deformation of the groove structure in the soft lacquer disk, temporary elastic deformation is also occurring, with the groove structure sort of collapsing under the stylus pressure while the disk is being played back. Even though the vertical tracking force is relatively low, even perhaps as low as 1.5 grams, the contact area of the stylus and groove is so small that the resulting point pressure is incredible. Just think in terms of pounds per square inch (PSI). The effect of this elastic and plastic deformation under the playback stylus is a reduction in the stylus’s ability to resolve fine detail. The final product, the vinyl record, is a much stronger, more durable material than a lacquer disk. However, the elastic and plastic deformation effects are still present, which is one of the major differences one can notice between the vinyl compounds used by different pressing plants, especially if, like me, you regularly get to compare the same master pressed at different pressing plants using different vinyl compound formulations.
The grooves of a vinyl record hide within them much more information than what we can ever extract out of them. This is where low vertical tracking force and a line contact stylus (which maximizes the area of contact between stylus and groove, reducing the PSI for a given value of VTF) come in handy.
Which brings us back to the paradox of the metal mother sounding better than the master disk it was produced from. It is not that the metal mother contains more information; it most probably contains a bit less. But a nickel disk is much harder than both a vinyl record and a master lacquer disk. A harder material can withstand much higher PSI values before deformation begins. As such, given identical playback conditions, the groove structure of the nickel mother will deform much less under the stylus pressure, which allows the extraction of fine detail that would be lost to deformation on a softer medium. Even if less information is stored in the grooves of the nickel mother compared to the lacquer master, so much more of it can be extracted again that we end up with more information being translated into an electrical audio signal for the loudspeakers to transform to sound. Not being infinitely rigid, the nickel mother also suffers deformation, but to a much lesser extent compared to a much softer lacquer master or vinyl record.
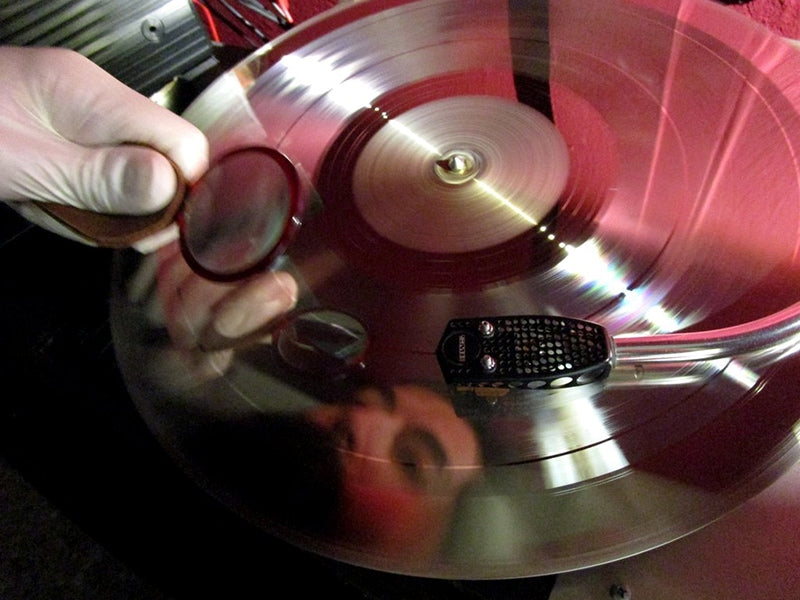
A metal mother disk. Courtesy of Agnew Analog Reference Instruments.
Realizing this many years ago, I have been considering ideas such as releasing high-fidelity recordings on nickel mothers instead of vinyl records, or in addition to a conventional vinyl LP release. However, there are several technical challenges that have been stopping me from doing so.
The first problem is that the center of the lacquer master disk cannot be transferred to the nickel mother, so the nickel mother would need to somehow be centered accurately. The second and closely-related problem is that the center hole of the nickel mother is typically larger than an LP center hole (but smaller than a large-hole 7-inch single), which makes it incompatible with normal turntable platters without major surgery.
The third problem is that due to the internal stresses incurred in manufacturing the thin nickel disk, it is usually far from flat. A vacuum suction platter could be used for playback, to flatten it out, but how many turntables (and audiophiles) are so equipped?
The fourth problem is the cost. A well-made nickel mother is already several orders of magnitude more expensive than a vinyl record, even before attempting to solve all the aforementioned issues. Once you do solve them, the cost would be astronomical.

Courtesy of Agnew Analog Reference Instruments.
Lastly, nickel mothers come with an inherent problem that cannot be solved: nickel is ferromagnetic, and most moving coil playback cartridges have a strong enough stray magnetic field on their underside that this field would attract the cartridge to the nickel mother with considerable force, making it impossible to maintain the VTF setting. Playback of the ultra-expensive nickel mothers would therefore be limited to moving magnet or moving iron designs with very low leakage flux on their underside. Other than that, it would have been a great idea, to fully showcase the information storage capabilities of the disk medium, in a way which facilitates the successful extraction of as much of this information as would be possible.
Enter the DMM Dubplate Vol. 1. As previously discussed, the DMM process can directly produce a metal mother right there on the disk mastering lathe, with no further steps required. Not only does this eliminate the possibility for any losses between the mastering stage and a subsequent electroplating process, but it also comes with the correctly-sized center hole to fit a conventional turntable platter, and since the mother is cut on the lathe, its accurate centering is maintained!

The Neumann VMS-82 cutting lathe at Stockfisch Records.
The blank disks used for the DMM process are made of austenitic stainless-steel substrates, plated with a layer of copper phosphate. None of these materials is ferromagnetic, affording total freedom in the selection of a playback cartridge for the DMM Dubplate.
Naturally, there are challenges to making this happen. While the center hole and centering are no problem, the normal DMM blanks are 14 inches in diameter, instead of the usual LP size of 12 inches. The flatness is not tightly controlled, as they are normally kept flat by the suction of the Neumann VMS-82 cutting lathe’s vacuum platter (the VMS-82 is the cutting lathe used by Stockfisch Records, and the only disk mastering lathe designed specifically for the DMM process). DMM disks are also considerably thicker than a vinyl record, not to mention heavier. The team at Pauler Acoustics tackled these challenges by creating a DMM disk that is just over 12″ in diameter, able to fit on any turntable. They do their own, in-house flatness quality control, so only the truly flat DMM blanks are used for making DMM dubplates. The DMM dubplates remain thicker and heavier than a vinyl record, but this shouldn’t be an issue on any reasonable turntable.
As the DMM disks are cut on a lathe, the process leaves absolutely no room for mass production methods. The DMM dubplates have to be cut one by one on a lathe, in real time, by a real human. As such, each one is unique, with the customer’s name handwritten on the label. I shouldn’t have to point out that this is a very time-consuming and expensive process, requiring skill, passion, experience and extremely rare equipment. In view of this, while the cost of the DMM Dubplate Vol. 1 is much higher than a vinyl record or even a master tape copy, knowing what is involved in making it, I feel it is very reasonably priced, if not an outright bargain. That was before I got to listen to it…
One morning, the daily row of courier drivers that deliver and collect packages, pallets and crates to and from our premises, brought the package in that contained the DMM Dubplate Vol. 1. It was a relatively small size (the courier driver being more accustomed to having to lower 2,000 lb. crates using the hydraulic tailgate of their 18-ton truck), did not draw much attention, and the unsuspecting driver probably won’t even remember the significance of this package, but I will not easily forget the hours of staring at the package, unable to open it due to our policy of putting all incoming packages on a 48-hour quarantine to keep our workforce safe in times of pandemic.
In the next episode, you may get to find out what happened after I did listen to it…if you’re lucky!