How are the ancient Egyptians, Archimedes, Leonardo Da Vinci, and Henry Maudslay related to sound recording?
There are inventions that make us wonder how anyone could have come up with such an idea. Sound recording is perhaps one of them. Considering the historical context, however, we shall observe that it was not actually such a crazy or far fetched idea, given the technology available at the time.
In the late 19th century, most of the world had no access to electricity. The concept of electronic amplification would still need almost half a century to establish itself as a viable technology. Steam engines were very popular prime movers in the industry. But, even for the steam engine to become a viable reality, what was required were the appropriate machine tools, allowing the manufacture of accurate parts for a variety of purposes.

Machine screws, used as fasteners.
By no means a recent invention, machine tools in more primitive forms have existed for many centuries. The “prehistoric lathe” is perhaps one of the earliest predecessors to the lathe commonly used at present.



An illustration dating from 1395, showing what is known as the pole lathe.
Another ancient innovation of particular significance was the screw, described by Archimedes in 234 BC, after his visit to Egypt. It was not used as a fastener, but as an ingenious way to pump water. Ancient screws were rather crude by modern standards, often constructed by primitive means.

An illustration of the screw pump described by Archimedes in 234 BC. This concept was already in use in Egypt, from where it passed on to Greece.
By 1483, illustrations were depicting screw-cutting lathes operating on principles remarkably similar to present-day lathes. Leonardo Da Vinci had also designed one by 1500.
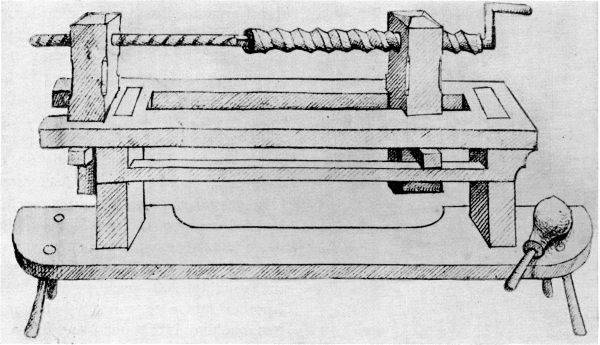

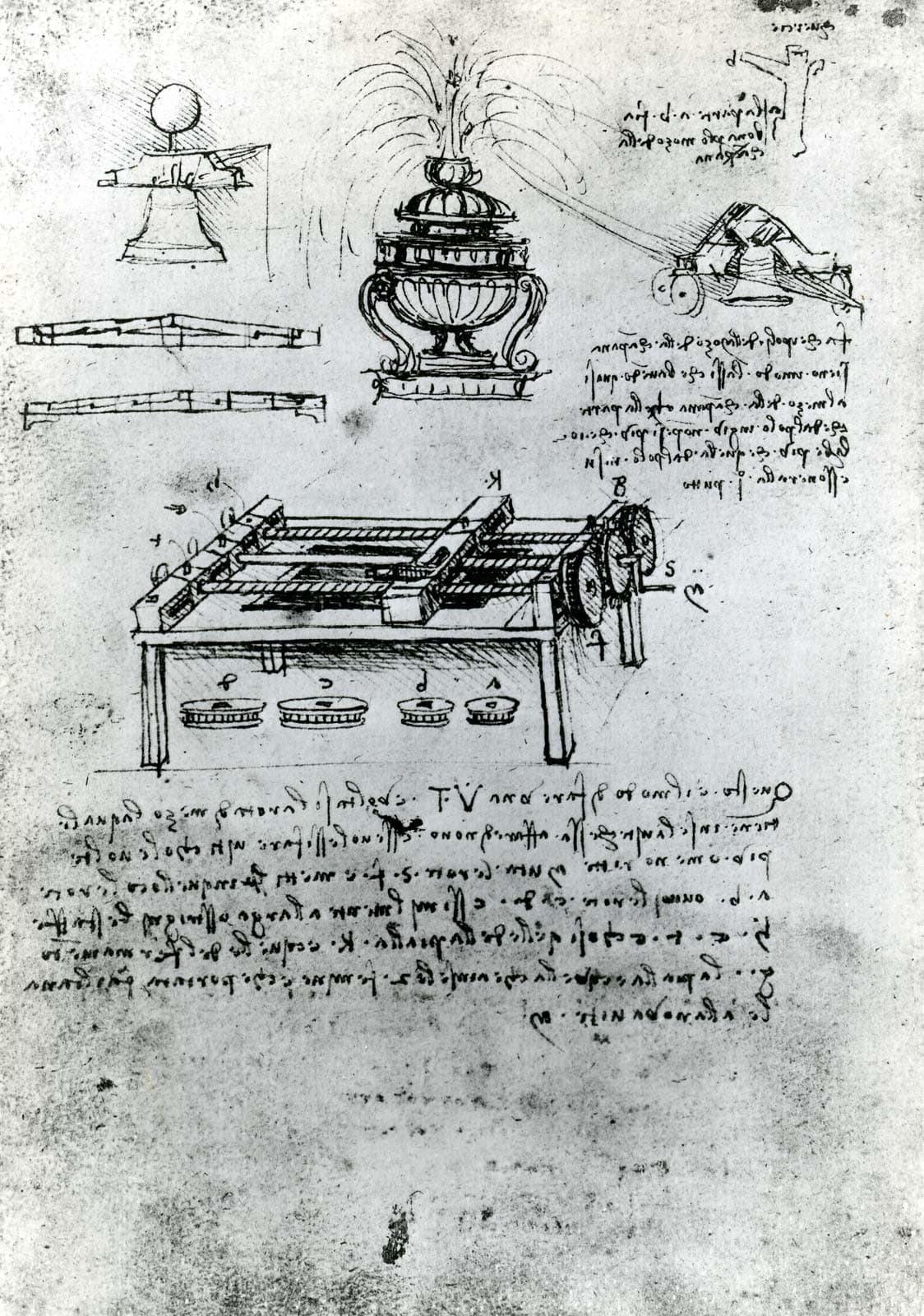
A screw-cutting lathe designed by Leonardo Da Vinci around 1500.
Henry Maudslay had built a fine example in England around 1800 and by that time, it was becoming more and more common to make precise screws for use in measurement instruments as the measuring element, using screw-cutting lathes.

Screw-cutting lathes built by Henry Maudslay between 1797 and 1800, in England.
Screws were also used as a means of advancing the carriage holding the cutting tool, longitudinally or transversely, on lathes.

A much more advanced lathe, dating from 1911. If properly cared for, lathes from the early 20th century can still be found in working condition, with the better examples putting to shame many modern lathes in terms of accuracy.
In such applications, they are called leadscrews or feedscrews and any shortcomings in the manufacture of such screws translate to loss of accuracy in the work done on that lathe.
The most popular and usually much less demanding application for screws is as threaded fasteners, holding the world together, or rather, the world’s mechanical assemblies. Screws are literally everywhere, made from a huge variety of different materials and come in sizes ranging from “so tiny you’d need magnification to see it”, to “so large you’d need a crane to lift it”.
It usually begins with smooth, cylindrical bar stock of the desired material, which is being held and rotated by the lathe, while a cutting tool of suitable geometry cuts the thread, advancing at the appropriate rate in relation to the rotational speed, to derive the desired thread pitch. The depth of cut is a critical parameter.
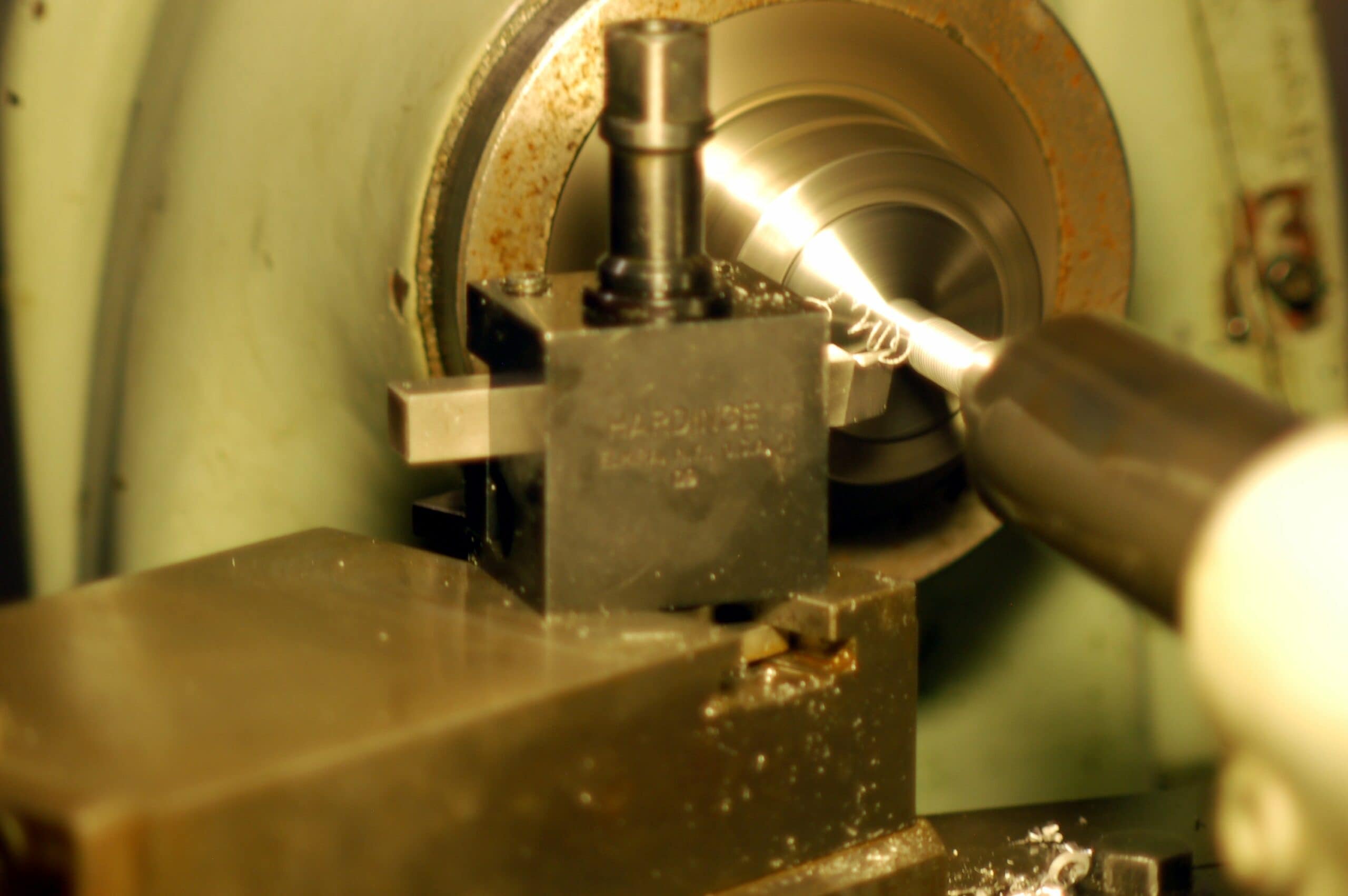

Almost completed screw, held on the lathe, awaiting the final finishing pass. Note the geometry of the cutting tool, required to form the thread and the resulting chip (the material removed). The cutting tool used to cut phonograph records is of similar geometry, but considerably smaller. Photograph courtesy of Agnew Analog Reference Instruments. While screws can be cut in multiple passes, a record has to be cut in one pass.
Let us assume we have a certain nut and we need to make a screw to work with it. We can easily figure out the approximate size and pitch, but if we cut the thread too deep, there will be excessive play between screw and nut. If we do not cut the thread deep enough, it won’t even screw on, due to inadequate clearance. We can therefore see that the depth of cut must not only be correct, but also constant. If we were to continuously vary the depth, it would be impossible to use that screw with any nut.
However, we could use a measurement instrument with a stylus if we want to measure any such variation in depth…Wait… So, what if we were to intentionally vary the depth during the cut, in proportion to sound? Then we could use a stylus to “measure” these variations, converting them back into sound!
I assume Thomas Edison must have thought something along these lines when he invented his variable-depth screw-cutting lathe, known as the “phonograph”!

Thomas Edison with his phonograph, around 1878.
Well aware of the recent technological developments in the field of machine tools, as an inventor, he took the concept of a screw-cutting lathe and added the variable-depth feature, modulating the depth of cut around the base value of a silent groove, by means of the acoustic energy reaching a diaphragm at the throat of the horn. A stylus was attached to the other end of the diaphragm, translating the motion of the diaphragm into a deeper or shallower thread. It was an entirely mechanical process and so was the playback. To reproduce the recording, the change in depth would push a stylus attached to a diaphragm, thereby translating the depth change into air pressure variations, with the diaphragm acting upon the air within the horn. This would produce sound, in the exact reversal of the process which recorded the sound.
Sound recording started as vertically modulated grooves on a cylinder, as this was the most obvious way of doing it, in consideration of the parallels with machine tool development. It was also the simplest way of doing it without needing overly elaborate mechanisms. The cylinder was just a screw, cut on a lathe, with the addition of a diaphragm and stylus, in place of the stationary cutting tool used to cut ordinary “silent” screws.
But, are ordinary screws really silent? As you will discover if you try to play back a screw, as if it were a recording, the majority of screws are far from silent! Since most machine tools were not designed for sound recording, little effort was made to prevent the sounds of the machine itself from being recorded onto the screws it was cutting!
However, where extreme accuracy was required, precision machine tools were used, designed to not allow any unintentional errors to make it to the workpiece. While this level of precision is not normally found in ordinary screws used as fasteners, the finest leadscrews are made in ways which make them quieter upon playback, should you decide to discover the secret world of unintentional sound recordings as a by-product of industrial manufacturing processes. Which is probably also where the origins of sound synthesis and electronic musical instruments could be traced.
Phonograph cylinders were the humble beginning of the recording industry, which grew enormously and changed dramatically since those early days. New technologies, then and now, rarely come out of nowhere. They are usually based on the collective body of knowledge and experience already established by others, often in seemingly unrelated sectors.
Progress mostly occurs in small logical steps, to address certain needs. Over a century prior to the invention of sound recording and subsequent reproduction, there were already documented attempts to do so. The most widely known example, the phonautograph of Édouard-Léon Scott de Martinville (1857), went as far as graphically representing sound, but with no possibility of reproduction as sound. The phonograph cylinder was the first invention that succeeded in being able to reproduce sound.


A phonautogram, which is what the phonautograph could do, dating from 1859.
In the next episode, we shall investigate the transition from the cylinder to the disk record.